Düsseldorf
Bonner Str. 367-371
40589 Düsseldorf
Phone:+49 211 515 81 70
Fax:+49 211 515 81 728
Email: info@trade-world-one.de
Vienna
Rathausstrasse 21/12
1010 Vienna
Phone: +43 664 171 89 69
Email: kontakt@trade-world-one.at
Seat frames: The invisible backbone for passenger comfort and operational safety
In the public perception of public transport vehicles - be it streetcars, subway trains, regional trains or buses - the focus is often on aspects such as drive technology, punctuality or the design of the passenger cabin. Components that work behind the scenes are rarely appreciated. One of these critical, often underestimated components are seat frames. For the layman, it is simply a support for the seat shell and upholstery. For us as engineers, procurement experts and operators, however, it is a highly complex component that acts at the interface of safety, durability, passenger comfort, lightweight construction and, last but not least, the economic efficiency of a vehicle.
Do you have any questions? Feel free to contact us at any time.
» To the contact pageAt Trade World One, we understand that the excellence of a transportation system lies in the details. Our DNA, shaped by decades of experience in senior procurement roles at global technology leaders such as SIEMENS, has taught us to look beyond the mere component. We do not see seat design as a catalog product, but as a technical solution whose specification, materiality, production and life cycle management are decisive for the operational readiness and total cost of ownership of a vehicle. This article is intended to shed light on the complex technical requirements for seat frames and show how a strategic procurement approach can master the challenges of modern transportation companies.
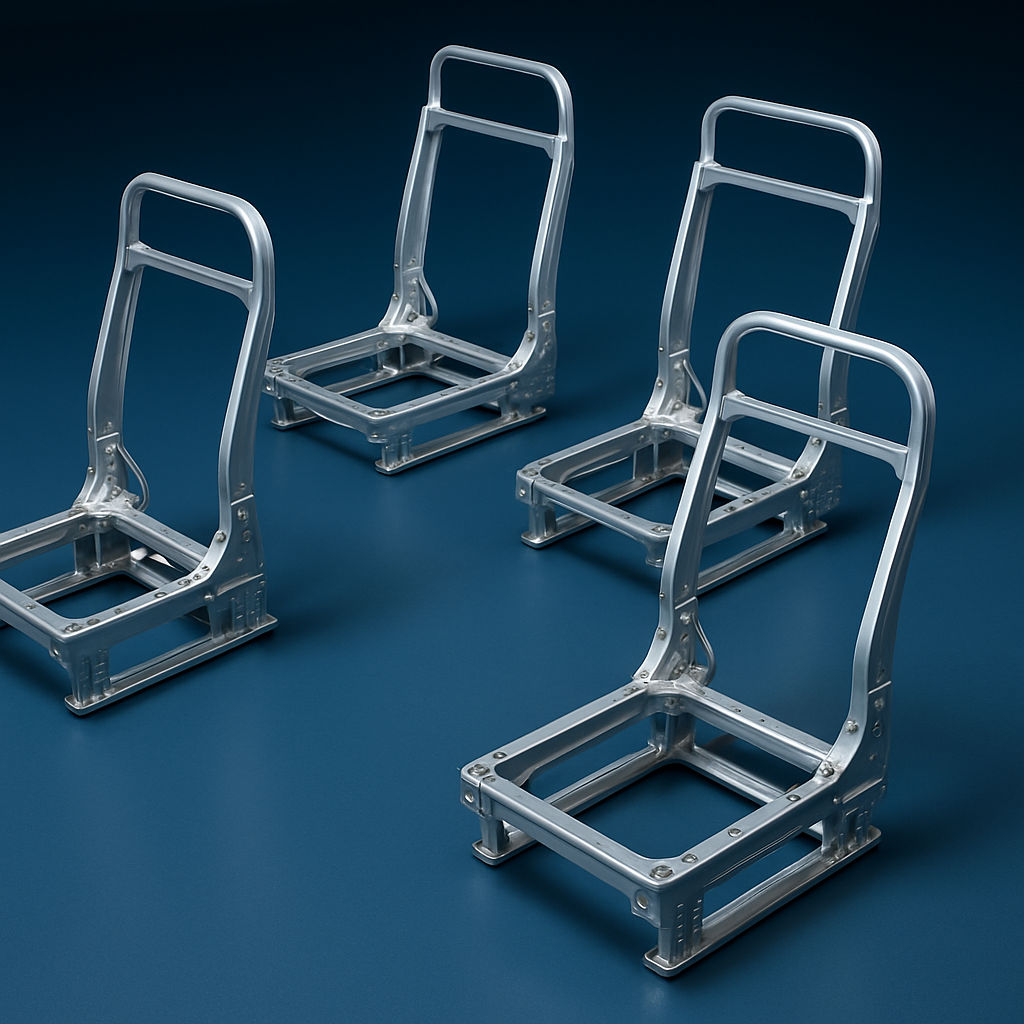
Material science for durable seat frames: the right choice of material as a foundation
Choosing the right material for a seat frame is not a trivial decision. It is a fundamental compromise between weight, strength, corrosion resistance, cost and workability. Each material class has specific advantages and disadvantages that need to be carefully weighed up in the context of the respective application scenario.
Steel and its alloys:
The classic material for the seat base is and remains steel. Unalloyed structural steels such as S235JR are still widely used due to their excellent weldability, high availability and low price, especially in vehicles where weight plays a subordinate role or which are designed for maximum robustness. Higher-strength steels are used for more demanding lightweight construction concepts. These make it possible to reduce wall thicknesses and thus achieve significant weight savings while maintaining or even increasing strength. The decisive disadvantage of standard steels is their susceptibility to corrosion. Therefore, high-quality surface protection, for example by cathodic dip coating (CDC) followed by powder coating, is essential for every seat support.
Stainless steel - aesthetics and durability:
Where durability, hygiene and a high-quality appearance are paramount, stainless steel is the first choice for a frame construction for seats. Austenitic stainless steels, such as the material 1.4301 (V2A) or the even more corrosion-resistant 1.4404/1.4571 (V4A), do not require any additional coating. Their passive layer protects them permanently against corrosion. The brushed or polished surface is also resistant to scratches and vandalism. The disadvantages lie in the higher material costs and the more demanding processing, especially when welding, which requires special procedures and specialist knowledge.
Aluminum - the lightweight construction champion:
Lightweight construction is a key issue in modern rail vehicle and bus construction. Every kilogram saved reduces energy consumption. This is where aluminum really comes into its own as a material for seat frames. Aluminum alloys offer an excellent strength-to-weight ratio. The extrusion process also allows highly complex and functionally integrated profiles to be produced, which reduces the number of components and assembly costs. The challenges with aluminum lie in its lower fatigue strength and the need for special welding processes. As your technical procurement partner, we at Trade World One know exactly which global suppliers have the expertise for the reliable processing of such seat brackets.
Fiber composites and plastics:
Although less frequently used for the primary load-bearing structure of seats, fiber composites and high-strength plastics are gaining in importance, especially for seat shells. They offer maximum design freedom and low weight. However, their use in the primary load-bearing area is still the exception due to complex strength tests.
Constructive excellence of seat frames: Requirements for design, safety and durability
A seat frame is much more than a simple welded construction. It is a safety-relevant component that must meet strict standards and high functional requirements.
Crash safety and fastening:
The top priority is the crash safety of passengers. Seat frames must be designed in such a way that they can withstand the forces that occur in the event of a collision. The seat attachment and the attachment points on the vehicle floor or side wall are of crucial importance. In rail vehicles, the strength of passenger seats and their anchorages is subject to specific standards, which must be verified by FEM simulations.
Vandalism resistance and durability:
In public spaces, resistance to vandalism is a constant challenge. This means robust designs and the use of tamper-proof screw connections. The surfaces must be scratch, impact and cleaning agent resistant in order to maintain an attractive appearance over a life cycle of 20 to 30 years.
Ergonomics and modularity:
Although ergonomics are primarily determined by the seat upholstery and shell, the frame for seats sets the basic parameters. In addition, modularity is a key factor for cost-effectiveness. Modern seat frame systems are often designed as a modular system, which simplifies assembly and the storage of spare parts.
System integration:
The seat carrier is not an isolated component, but a platform for integrating additional functions such as monitors, USB charging sockets or waste garbage cans. A forward-looking design provides standardized interfaces for this purpose.
Production processes for seat frames: from specification to quality assurance
Turning an excellent design into a reliable series product requires controlled manufacturing processes. As an ISO 9001-certified company, we at Trade World One place the highest value on the process reliability of our suppliers.
Manufacturing process:
The manufacture of a seat base frame involves a chain of precise processing steps. The central process is welding. Certification in accordance with EN 15085 is essential for welding work on components for rail vehicles. This standard defines the quality requirements and ensures that safety-relevant components such as seat frames are manufactured in a reliable process. Our global network only includes suppliers who can provide evidence of this certification.
Surface treatment and assembly:
Welding and grinding are followed by surface treatment (cathodic dip coating and powder coating), which protects the seat frame from corrosion and gives it the desired appearance and durability. Final assembly and quality control complete the process.
Procurement & lifecycle management: The strategic dimension of the seat frame
This is where Trade World One's core competence lies. We understand that our customers' challenges often only begin once the vehicle is in operation.
The challenge of obsolescence:
After 15 or 20 years, it is not uncommon for the original seat manufacturer to no longer exist. A damaged seat frame can therefore become a serious problem and make the strategic procurement of spare parts more difficult.
Our solution: reverse engineering and production based on samples:
We have perfected our processes for precisely these cases. A customer sends us a sample of the defective or obsolete seat frame. Our team of engineers starts a precise reverse engineering process. We create complete, production-ready drawing documentation and commission a certified partner with the production. This process not only ensures the availability of spare parts, but also ensures that the new seat design complies with current standards.
Global procurement and resilient supply chains:
The experience of our founder, Rainer Schieck, from his time as Head of Purchasing at SIEMENS is deeply rooted in our DNA. We know the global procurement markets and know where to find certified quality for every type of seat base at competitive conditions.
The future of seat construction: intelligent and sustainable solutions
The development of the seat frame is not standing still, driven by digitalization and sustainability.
Intelligent seats:
The integration of sensors for utilization control and charging infrastructure will increase. The frame for seats will become an intelligent infrastructure platform.
Sustainability and circular economy:
The pressure to reduce the carbon footprint promotes the use of recycled1 materials. Seat frames made from recycled aluminum or steel will become increasingly important.
Digitalization in maintenance:
In future, every seat frame could be linked to a digital twin. A QR code on the component takes the maintenance technician directly to all relevant information and solves the problem of missing documentation.
Conclusion: More than just a carrier - the seat frame as a strategic component
The seat frame is a prime example of a component whose complexity and strategic importance remain hidden at first glance. It is a safety-relevant component, a decisive factor for operating costs and a central element of the passenger experience. The right choice of material, design and manufacturing partner have far-reaching consequences for the entire life cycle of a vehicle.
At Trade World One, we go beyond the role of a mere supplier. With our deep industry DNA and commitment to certified quality, we are your technical problem solver. Whether it's a new development for a fleet of vehicles or the reproduction of an obsolete seat frame without drawings, we understand your challenges. We don't just supply components. We deliver solutions, availability and the technical safety you need for the reliable operation of your transportation systems. For us, the seat frame is not just a piece of metal, but a promise - the promise of quality, safety and reliability. That is precisely our mission.
Sources
- Development of a method for optimizing seating comfort on car seats - Dissertation of the Technical University of Munich
- The science of sitting - Scientific study by ETH Zurich on the influence of seating mechanics on health
- Influence of non-adapted school furniture on musculoskeletal pain - Bachelor thesis, HAW Hamburg
- Scientific studies on dynamic sitting and ergonomic chairs - Dauphin
- Sitting at school - Max Delbrück Center research project to record sitting behavior in children
- Study on sitting times of adults in Germany - Health monitoring of the Robert Koch Institute (RKI)
- Scientific Review on Sitting Posture and Ergonomics - National Center for Biotechnology Information (NCBI)
- Research on Ergonomic Seat Design and Pressure Distribution - ScienceDirect Journal
- Effects of Seating Postures on Spinal Health - Frontiers in Neurology
- Ergonomics and Musculoskeletal Disorders Related to Seating - SpringerLink
Do you have any questions? Feel free to contact us at any time.
» To the contact page