Düsseldorf
Bonner Str. 367-371
40589 Düsseldorf
Phone:+49 211 515 81 70
Fax:+49 211 515 81 728
Email: info@trade-world-one.de
Vienna
Rathausstrasse 21/12
1010 Vienna
Phone: +43 664 171 89 69
Email: kontakt@trade-world-one.at
Hot pressing process for GRP: Efficient production of fiber composite components
Hot pressing process for GRPModern production for high-quality fiber composite components, which is becoming increasingly important in many branches of industry, especially in transport and environmental technology. This process enables the efficient production of robust, lightweight and dimensionally stable Fiber composite components with excellent surface quality. Trade World One, as a specialized technical procurement partner, supports customers with comprehensive expertise in all aspects of GRP hot pressed components and their application.
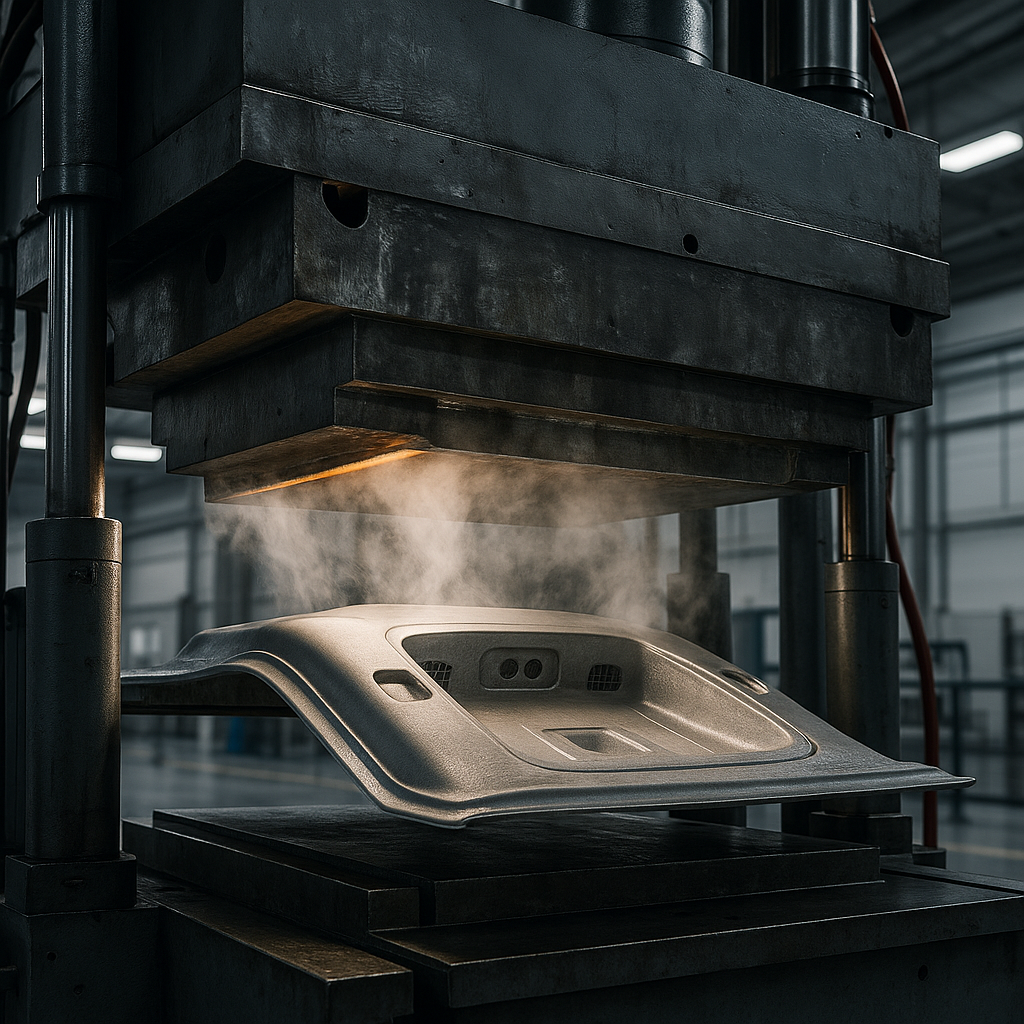
GRP hot pressed: Definition, properties & materials
Glass fiber-reinforced plastics are composite materials consisting of a plastic matrix and embedded glass fibers. With this form of Thermoset processing a plastic matrix - usually an unsaturated polymer - is Polyester resin (UP) for industrial applications or a high-strength Epoxy resin (EP) for high-performance parts - combined with glass fibers. The result is a Fiber composite materialwhich is particularly corrosion-resistant, lightweight and dimensionally stable. Typical properties of GRP are high strength combined with low weight, chemical resistance to aggressive media and good electrical insulation properties. These characteristics make GRP a preferred material in demanding technical applications.
Do you have any questions? Feel free to contact us at any time.
» To the contact pageThe hot pressing process for GRP: From SMC & BMC to the finished component
Hot pressingoften also referred to as Compression molding labeled, is a thermomechanical shaping process in which Pre-impregnated semi-finished products such as Sheet Molding Compound (SMC, also known as fiber resin mat) or Bulk molding compound (BMC, also known as fiber resin compound) are brought into a mold under defined conditions of temperature, pressure and time. Typical pressing parameters are temperatures between 130 and 180 °C, pressures of 50 to 250 bar and cycle times of a few minutes.
SMC material consists of flat glass fiber mats that are impregnated with a resin matrix mixture. It is particularly suitable for large, thin-walled components with a high surface quality. The pasty BMC material is ideal for complex, three-dimensional geometries and enables precise shaping. Both material types contain between 15 and 35 percent glass fiber, supplemented by mineral fillers and additives for improved processing and end product properties.
The compression molding process: steps in GRP production
In the production process, the prepared material is first cut to size (for SMC) or metered (for BMC) and placed in a preheated forming tool. There, the material is shaped by high pressure and heat and at the same time the resin is cured, creating a permanent bond between the fibers and the matrix. During the process, air and gas inclusions are removed to ensure a homogeneous component structure. Immediately after pressing, the components can be demolded and, if necessary, mechanically reworked (e.g. deburring, drilling) or surface-finished (e.g. painting).
Advantages of hot-pressed GRP: Quality, efficiency & sustainability
The Compression molding offers a significant leap in quality compared to other manufacturing processes such as wet pressing or hand laminating. The closed mold technology produces high-quality, smooth surfaces on both sides without additional reworking. Automation and short cycle times ensure high efficiency while keeping material waste to a minimum. Excess material (flash) can be reused in recycling processes, in recycling processes, e.g. as a filler for new compounds or in cement production, for energy or material recycling. The mechanical properties of hot-pressed components are impressive due to their even fiber distribution and low porosity, which leads to improved strength values.
Hot-pressed GRP: Applications in transportation, industry & environmental technology
In the transport sector, hot-pressed Components for rail vehicles and commercial vehicles is a prime example of successful Lightweight construction. They are used for chassis components, interior structures such as seat frames or door panels as well as current collectors. In the field of electromobility, battery housings are also increasingly being used as robust Housing made of GRP realized. The combination of low weight and high mechanical strength improves the energy efficiency and durability of the vehicles.
In environmental technology, hot-pressed GRP components are used in particular where high corrosion resistance is required, for example as housings for flue gas filter systems, chemical-resistant containers or covers in sewage treatment plants. The long service life and resistance to aggressive media make GRP an economical alternative to metal components.
Quality assurance during hot pressing: Test methods for GRP components
The Quality assurance is a central component of production. A seamless GRP test ensures that every component meets the specifications. The following are used
Non-destructive testing (NDT): Methods such as ultrasound and thermography detect internal defects such as air pockets or delamination without damaging the component.
Mechanical test methods: Tensile or bending tests on test specimens are used to directly Strength verification and validate the mechanical characteristics of the material.
Imaging analyses: Computed tomography (CT) enables precise control of fiber orientation and homogeneous material distribution, which is crucial for the performance of the component.
All process data (pressure, temperature, time) is also logged to ensure complete traceability of each batch.
The future of GRP hot pressing: innovations & new materials
Development in the area of hot-pressed GRP components is currently focused on the integration of thermoplastic resin systems, which offer shorter cycle times and improved recycling options. Research is also being conducted into hybrid materials that combine local reinforcement with carbon fibers with the advantages of GRP. Digital technologies enable advanced process control and quality assurance, while integrated sensor technology allows new functions and condition monitoring during the pressing process.
Procurement & partners: Reliable delivery of hot-pressed GRP
Trade World One supports customers in transportation and environmental technology with solid material expertise and a global network of certified manufacturers for hot-pressed GRP components. Thanks to our comprehensive technical understanding and an efficient logistics center, we ensure the rapid availability of even complex or obsolete components. We offer individual procurement solutions including reverse engineering to ensure the operational reliability and service life of your systems. Our expertise makes us the ideal partner for demanding GRP procurement.
Conclusion: Why hot-pressed GRP is the right choice
Hot-pressed GRP combines the advantages of modern composite materials with an efficient manufacturing process that is ideal for a wide range of technical applications. The combination of lightweight construction, robustness and cost-effectiveness positions this material as a key technology for future-oriented industrial partners such as Trade World One and their customers.
Sources
- Glass fiber reinforced plastics (GRP) – Wikipedia
- Glass Fiber Reinforced Plastics – ScienceDirect
- Glass fiber reinforced plastics – Springer
- What is Glass Fiber Reinforced Plastic? – Materials Today
- Glass Fiber Reinforced Polymer Properties
- Glass Fiber Reinforced Polymer Composites for Structural Applications – Elsevier
- Glass Reinforced Plastics – ScienceDirect
- Fiber Reinforced Polymer – Wikipedia
- Glass Fiber Reinforced Composites – ChemistryViews
- Advantages of Glass Fiber Reinforced Plastics – Materials Today
Do you have any questions? Feel free to contact us at any time.
» To the contact page