Düsseldorf
Bonner Str. 367-371
40589 Düsseldorf
Telefon:+49 211 515 81 70
Fax:+49 211 515 81 728
E-Mail: info@trade-world-one.de
Wien
Rathausstraße 21/12
1010 Wien
Telefon: +43 664 171 89 69
E-Mail: kontakt@trade-world-one.at
CFK (Carbon): Der Hochleistungswerkstoff für Industrie und Mobilität
Carbonfaserverstärkter Kunststoff (CFK), oft auch als Carbon bezeichnet, hat sich als Hochleistungswerkstoff in zahlreichen Industriebranchen etabliert. Dieser Verbundwerkstoff kombiniert Carbonfasern mit einer polymeren Matrix – üblicherweise Epoxidharz – zu einem Material, das bei extrem geringem Gewicht außergewöhnliche mechanische Eigenschaften bietet.
Mit einer Dichte von etwa 1,6 g/cm³ und einer Zugfestigkeit von bis zu 3500 MPa übertrifft CFK konventionelle Metalle wie Stahl oder Aluminium um ein Vielfaches. Die spezifische Steifigkeit liegt um bis zu 60 Prozent höher als bei Aluminiumlegierungen, während das Gewicht rund 40 Prozent unter dem von Aluminium und etwa 75 Prozent unter dem von Stahl liegt. Diese Eigenschaften machen CFK insbesondere für Anwendungen attraktiv, bei denen Gewichtsreduktion bei gleichzeitig hoher struktureller Integrität entscheidend ist – von Luft- und Raumfahrt über Automobilbau bis hin zu industriellen Anwendungen.
Haben Sie Fragen? Treten Sie gerne jederzeit mit uns in Kontakt.
Zur KontaktseiteDer weltweite Markt für carbonfaserverstärkte Kunststoffe wächst mit einer prognostizierten jährlichen Rate von 11,6 Prozent und soll bis 2030 ein Volumen von 54 Milliarden US-Dollar erreichen. Dieser Wachstumspfad wird durch die zunehmende Nachfrage in Schlüsselindustrien sowie durch technologische Fortschritte in der Fertigungstechnologie getragen.
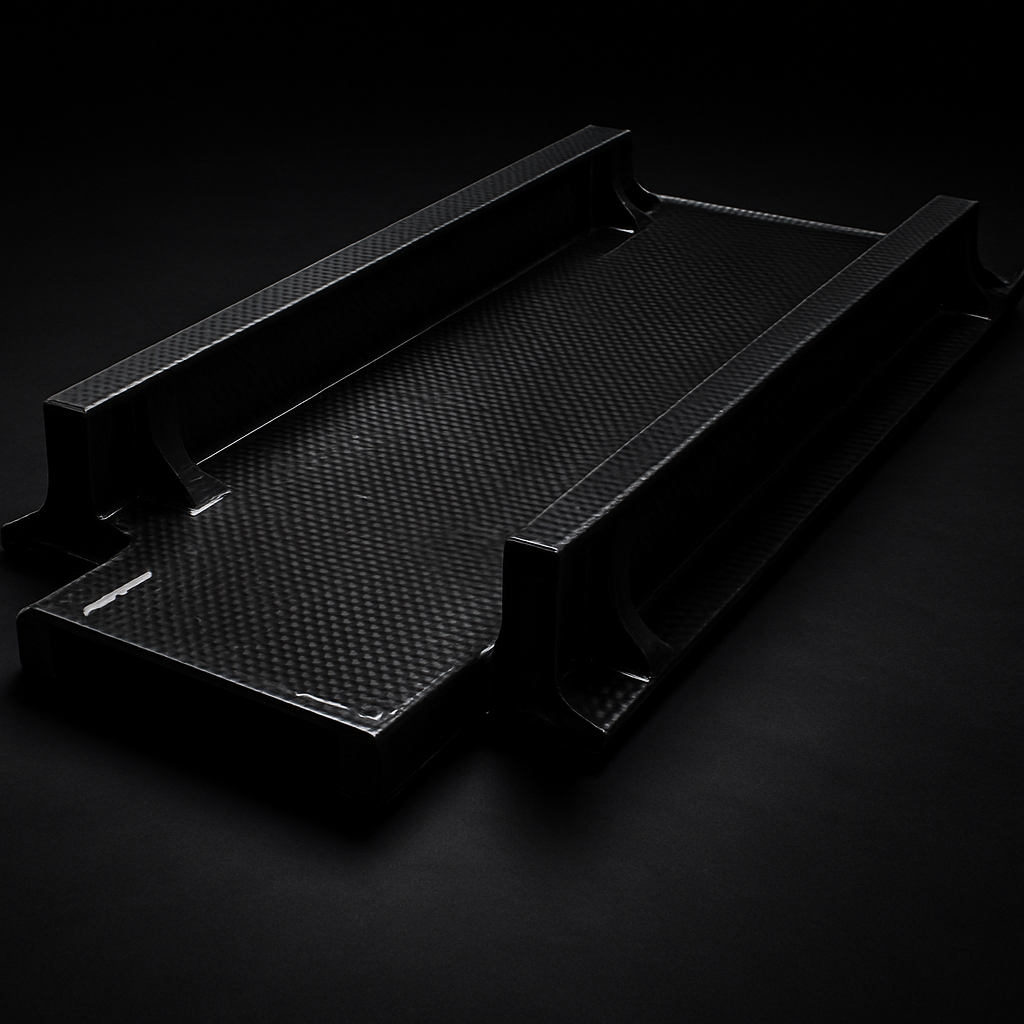
Grundlagen und Materialeigenschaften
CFK besteht aus Kohlenstofffasern mit einem Durchmesser von 5-10 Mikrometern, die in eine Kunststoffmatrix – meist Epoxidharz – eingebettet sind. Die Fasern werden durch Pyrolyse von Polyacrylnitril (PAN) bei Temperaturen von bis zu 1300°C unter Sauerstoffausschluss hergestellt, was zu einer nahezu reinen Kohlenstoffstruktur führt.
Die mechanischen Eigenschaften werden maßgeblich durch die kristalline Anordnung der Kohlenstoffatome bestimmt. Die Matrix hat dabei zwei Hauptfunktionen: Sie überträgt Kräfte zwischen den Fasern und schützt diese vor Umwelteinflüssen. Das resultierende Verbundmaterial zeigt eine ausgeprägte Anisotropie:
Zugfestigkeit: Bis zu 3500 MPa in Faserrichtung, jedoch nur etwa 50 MPa quer dazu.
Thermische Ausdehnung: Nahezu null in Faserrichtung (0,2·10⁻⁶ K⁻¹), aber deutlich höher quer dazu (30·10⁻⁶ K⁻¹).
Dieser Richtungseffekt erfordert eine präzise Auslegung der Faserorientierung im Bauteil, die mittels moderner Simulationsverfahren wie der klassischen Laminattheorie optimiert wird.
Produktionstechnologien
Die Fertigung von CFK-Bauteilen erfordert spezialisierte Verfahren:
Resin Transfer Molding (RTM): Trockene Faserhalbzeuge werden in einer geschlossenen Form mit Harz injiziert. Ideal für mittlere Stückzahlen und komplexe Geometrien.
Prepreg-Verfahren im Autoklaven: Vorimprägnierte Fasermatten werden unter hohem Druck und Temperatur ausgehärtet. Liefert höchste Materialqualitäten für die Luft- und Raumfahrt.
Same Qualified Resin Transfer Molding (SQRTM): Ermöglicht die Herstellung von Bauteilen in Autoklavenqualität ohne den energieintensiven Autoklavprozess.
Rapid Shaping Prozess: Kernmaterialien aus PU-Schaum werden mit Fasern ummantelt. Ideal für Prototypen und Kleinserien.
Industrielle Anwendungsfelder CFK
Verkehrstechnik und Mobilität
In der Verkehrstechnik revolutioniert CFK den Leichtbau.
Schienenfahrzeuge: CFK wird für Fahrwerkskomponenten und Dachstrukturen in Straßenbahnen und Elektrobussen eingesetzt, um Energieverbrauch und Achslasten zu reduzieren.
Automobilindustrie: Karosserieteile und Strukturverstärkungen in Hochleistungsfahrzeugen senken das Gewicht um bis zu 40 %. Zukünftig im Fokus: thermoplastische CFK (CFRTP) für die kostengünstige Großserienfertigung.
Wasserstofffahrzeuge: Type-IV-Druckbehälter aus CFK ermöglichen Betriebsdrücke von 700 bar bei 30 % Gewichtsersparnis gegenüber Aluminiumversionen.
Luft- und Raumfahrttechnologie
Die Luftfahrtindustrie ist Vorreiter in der Anwendung von CFK. Moderne Passagierflugzeuge wie der Airbus A350 bestehen zu über 50 % aus Carbon, was zu einer Gewichtsreduktion von bis zu 20 Tonnen führt und den Kerosinverbrauch signifikant senkt. In der Raumfahrt ermöglicht CFK leichte und extrem belastbare Satellitenstrukturen und Trägersysteme.
Industrielle und bautechnische Anwendungen
CFK spielt seine Vorteile besonders bei bewegten Massen aus.
Kranausleger: Bei gleicher Tragfähigkeit wird die Spannweite um 30 % vergrößert.
Landwirtschaft: Breitere Arbeitsgeräte bei gleichbleibender Achslast erhöhen die Flächenleistung.
Windenergie: CFK-Rotorblätter ermöglichen Längen von über 100 Metern, was die Wirtschaftlichkeit von Offshore-Windparks massiv verbessert.
Warum ist CFK so teuer? Kosten und Wirtschaftlichkeit
Die hohen Kosten limitieren den breiten Einsatz von CFK.
Materialkosten: Carbonfasern kosten zwischen 15-40 Euro/kg und machen ca. 60 % der Bauteilkosten aus. Die Herstellung ist extrem energieintensiv.
Fertigungskosten: Verfahren wie die Autoklavaushärtung erfordern hohe Investitionen und lange Zykluszeiten.
Lösungsansätze umfassen kostengünstigere Precursormaterialien, Hochgeschwindigkeitsfertigungsverfahren (z.B. Hochdruck-RTM) und die Automatisierung durch robotergestütztes Tape-Legen.
Wie nachhaltig ist CFK? Recycling-Herausforderungen und Lösungen
Die Kreislauffähigkeit von duroplastischem CFK ist eine große Herausforderung. Aktuelle Recyclingverfahren fokussieren sich auf drei Pfade:
Pyrolyse: Erhitzen unter Sauerstoffausschluss, um die Matrix zu zersetzen und die Fasern zurückzugewinnen.
Solvolyse: Chemisches Auflösen der Matrix durch überkritisches Wasser oder Lösungsmittel.
Mechanisches Recycling: Zerkleinern zu Granulat für Spritzgussanwendungen.
Industrielle Pioniere wie CFK Valley Stade Recycling liefern bereits recycelte Fasern mit bis zu 95 % der ursprünglichen Festigkeit. Zukünftig gewinnen thermoplastische Matrixsysteme an Bedeutung, da sie einfacher zu recyceln sind.
Sicherheitsrisiken bei CFK: Von der Verarbeitung bis zur Unfallrettung
Verarbeitung: Bei der Bearbeitung entstehen feine Faserpartikel, die lungengängig sein können und ein Gesundheitsrisiko ähnlich wie Asbest darstellen. Effektive Absauganlagen und persönliche Schutzausrüstung sind zwingend erforderlich.
Unfallrettung: Konventionelle Rettungsgeräte (z.B. Spreizer) können an den hochfesten CFK-Strukturen scheitern. Rettungskräfte benötigen spezielle Schulungen und Werkzeuge.
Beschaffungsstrategien und Lieferkettenmanagement
Die Beschaffung von CFK-Komponenten ist komplex, da sich die Produktion auf wenige Hersteller konzentriert. Eine ISO 9001-zertifizierte Beschaffung ist entscheidend.
Herausforderungen: Lieferengpässe, fehlende Dokumentationen bei Ersatzteilen, Qualitätssicherung.
Lösungen: Ein technischer Beschaffungspartner wie Trade World One sichert die Versorgung durch strategische Lagerhaltung (1.500 m² Lager für Halbzeuge), ein globales Lieferantennetzwerk, Reverse Engineering für Altsysteme und 3D-Scanning für die Reproduktion von Teilen ohne Zeichnung.
Umgang mit speziellen Beschaffungssituationen
Besondere Herausforderungen entstehen bei der Beschaffung von Ersatzteilen für veraltete Systeme oder bei Dokumentationslücken. Hier ermöglicht das Reverse Engineering durch erfahrene Ingenieure die Rekonstruktion fehlender Spezifikationen und die Fertigung identitätsgleicher Austauschteile. Bei Lieferantenausfällen etablierter CFK-Komponenten bietet das globale Netzwerk von Trade World One Zugang zu alternativen Fertigungskapazitäten. Für Sonderanfertigungen ohne Zeichnungsvorgabe kommen moderne Bemusterungstechniken zum Einsatz, die auf 3D-Scanning und digitalen Zwillingen basieren. Diese Verfahren gewährleisten eine maßgenaue Reproduktion auch bei komplexen Geometrien, wie sie in der Verkehrstechnik bei Bremsgestängen oder Radsatztragern vorkommen. Die Kombination aus technischem Know-how und globaler Beschaffungskompetenz schafft so Lösungen auch in kritischen Versorgungssituationen.
Marktentwicklung und zukünftige Trends von CFK
Der globale Markt wächst dynamisch, angetrieben durch erneuerbare Energien, Wasserstoffspeicherung und E-Mobilität. Technologische Innovationen zielen auf:
Kostensenkung: Günstigere Fertigungsverfahren sollen Carbon für den Serienbau zugänglich machen.
Funktionsintegration: Sensorfasern zur Echtzeit-Überwachung der Bauteilintegrität (Structural Health Monitoring).
Verbesserte Eigenschaften: Selbstheilende Matrixsysteme und nanomodifizierte Harze zur Erhöhung der Schlagzähigkeit.
Fazit und Ausblick
Carbonfaserverstärkter Kunststoff (CFK) ist ein unverzichtbarer Hochleistungswerkstoff für moderne Industrien. Seine einzigartige Kombination aus geringem Gewicht und hoher Festigkeit ermöglicht wegweisende Innovationen. Trotz Herausforderungen bei Kosten und Recycling wird Carbon seine Position als Schlüsselmaterial für nachhaltige und effiziente Technologielösungen weiter ausbauen. Eine zuverlässige, technisch versierte Beschaffung ist dabei der entscheidende Faktor, um die Potenziale dieses Werkstoffs voll auszuschöpfen und Produktionsrisiken zu minimieren.
Quellen
- IPA Journal 02/2024: CFK Recycling – Forschung zu Kohlefaserverstärkten Kunststoffen und deren Toxizität
- Entsorgung faserhaltiger Abfälle – Umweltministerkonferenz PDF zu Recycling und Verbrennung von Carbonfasern
- Gesundheitsgefährdung durch lungengängige Kohlenstofffasern bei Brand von Carbonkunststoffen
- IMK Bericht Nr. 177: Grundlagen zu Faserverbundwerkstoffen und CFK – Brandschutz und Faserausbreitung
- Tragfähigkeit von CFK-Metall-Laminaten unter mechanischer und thermischer Belastung – Wissenschaftliche Untersuchung der Werkstoffeigenschaften
- ScienceDirect Artikel zu Herstellung und Eigenschaften von CFK-Materialien in der Leichtbautechnik
- Springer Fachkapitel: Werkstoffkunde und Anwendungen von carbonfaserverstärkten Kunststoffen
- ResearchGate: Überblick zu CFK-Verarbeitungsmethoden und mechanischen Eigenschaften
- Wissenschaft.de Bericht: Die Leichtigkeit des CFK – Verwendung und Vorteile von Kohlefaserverbundstoffen
- Materialwissenschaften.de: Grundlagen zu CFK-Faserverbundwerkstoffen – Struktur und Anwendung
Haben Sie Fragen? Treten Sie gerne jederzeit mit uns in Kontakt.
Zur Kontaktseite