Düsseldorf
Bonner Str. 367-371
40589 Düsseldorf
Telefon:+49 211 515 81 70
Fax:+49 211 515 81 728
E-Mail: info@trade-world-one.de
Wien
Rathausstraße 21/12
1010 Wien
Telefon: +43 664 171 89 69
E-Mail: kontakt@trade-world-one.at
Heißpressverfahren für GFK: Effiziente Fertigung von Faserverbund-Bauteilen
Heißpressverfahren für GFK: Moderne Fertigung für hochwertige Faserverbundkomponenten, die in vielen Industriezweigen, insbesondere in der Verkehrs- und Umwelttechnik, zunehmend an Bedeutung gewinnt. Dieses Verfahren ermöglicht die effiziente Herstellung von robusten, leichten und formstabilen Faserverbundkomponenten mit exzellenter Oberflächenqualität. Trade World One, als spezialisierter technischer Beschaffungspartner, unterstützt Kunden mit umfassendem Know-how rund um GFK heißgepresst Komponenten und deren Anwendung.
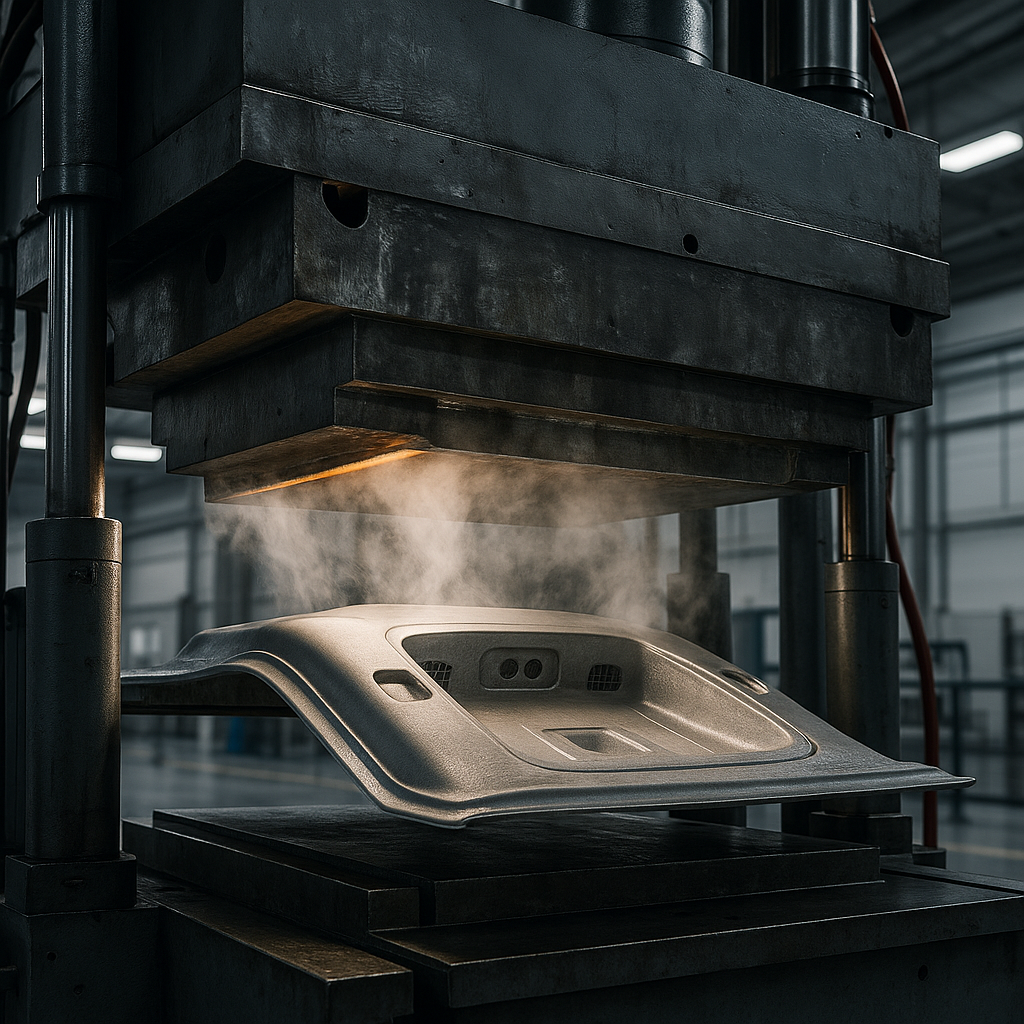
GFK heißgepresst: Definition, Eigenschaften & Werkstoffe
Glasfaserverstärkte Kunststoffe sind Verbundwerkstoffe, die aus einer Kunststoffmatrix und eingelagerten Glasfasern bestehen. Bei dieser Form der Duroplast-Verarbeitung wird eine Kunststoffmatrix – meist ein ungesättigtes Polyesterharz (UP) für industrielle Anwendungen oder ein hochfestes Epoxidharz (EP) für Hochleistungsteile – mit Glasfasern kombiniert. Das Ergebnis ist ein Faserverbundwerkstoff, der besonders korrosionsbeständig, leicht und formstabil ist. Typische Eigenschaften von GFK sind hohe Festigkeit bei geringem Gewicht, chemische Widerstandsfähigkeit gegenüber aggressiven Medien sowie gute elektrische Isolationseigenschaften. Diese Merkmale machen GFK zu einem bevorzugten Werkstoff in anspruchsvollen technischen Anwendungen.
Haben Sie Fragen? Treten Sie gerne jederzeit mit uns in Kontakt.
Zur KontaktseiteDer Heißpressprozess für GFK: Von SMC & BMC zum fertigen Bauteil
Das Heißpressen, oft auch als Formpressen bezeichnet, ist ein thermomechanisches Formgebungsverfahren, bei dem vorimprägnierte Halbzeuge wie Sheet Moulding Compound (SMC, auch Faserharzmatte genannt) oder Bulk Moulding Compound (BMC, auch Faserharzmasse bezeichnet) unter definierten Bedingungen von Temperatur, Druck und Zeit in eine Form gebracht werden. Typische Pressparameter liegen bei Temperaturen zwischen 130 und 180 °C, Drücken von 50 bis 250 bar und Zykluszeiten von wenigen Minuten.
SMC-Material besteht aus flächigen Glasfasermatten, die mit einem Harzmatrixgemisch imprägniert werden. Es eignet sich besonders für großflächige, dünnwandige Bauteile mit hoher Oberflächengüte. Das pastöse BMC-Material ist ideal für komplexe, dreidimensionale Geometrien und ermöglicht eine präzise Formgebung. Beide Materialtypen enthalten Glasfaseranteile zwischen 15 und 35 Prozent, ergänzt durch mineralische Füllstoffe und Additive für verbesserte Verarbeitungs- und Endprodukteigenschaften.
Ablauf des Formpressens: Schritte der GFK-Fertigung
Im Fertigungsablauf wird das vorbereitete Material zunächst maßgerecht zugeschnitten (bei SMC) oder dosiert (bei BMC) und in ein vorgeheiztes Formwerkzeug eingelegt. Dort wird das Material durch hohen Druck und Wärme verformt und gleichzeitig das Harz ausgehärtet, was eine dauerhafte Verbindung zwischen Fasern und Matrix schafft. Während des Prozesses werden Luft- und Gaseinschlüsse entfernt, um eine homogene Bauteilstruktur zu gewährleisten. Sofort nach dem Pressen können die Bauteile entformt und bei Bedarf mechanisch nachbearbeitet (z.B. Entgraten, Bohren) oder oberflächentechnisch veredelt (z.B. Lackieren) werden.
Vorteile von GFK heißgepresst: Qualität, Effizienz & Nachhaltigkeit
Das Formpressen bietet gegenüber anderen Herstellungsverfahren wie Nasspressen oder Handlaminat einen deutlichen Qualitätssprung. Die geschlossene Werkzeugtechnik produziert beidseitig hochwertige, glatte Oberflächen ohne zusätzliche Nacharbeit. Die Automatisierung und kurze Zykluszeiten sorgen für hohe Wirtschaftlichkeit, während der Materialausschuss gering gehalten wird. Überschüssiges Material (Grat) kann in Recyclingprozessen, in Recyclingprozessen, z.B. als Füllstoff für neue Compounds oder in der Zementherstellung, energetisch oder stofflich weiterverwertet werden. Mechanisch überzeugen heißgepresste Bauteile durch eine gleichmäßige Faserverteilung und eine geringe Porosität, was zu verbesserten Festigkeitswerten führt.
Heißgepresstes GFK: Anwendungen in Verkehr, Industrie & Umwelttechnik
Im Verkehrssektor sind heißgepresste Komponenten für Schienenfahrzeuge und Nutzfahrzeuge ein Paradebeispiel für gelungenen Leichtbau. Sie kommen für Fahrwerksbauteile, Innenraumstrukturen wie Sitzrahmen oder Türverkleidungen sowie Stromabnehmer zum Einsatz. In der Elektromobilität werden zunehmend auch Batteriegehäuse als robuste Gehäuse aus GFK realisiert. Die Kombination aus geringem Gewicht und hoher mechanischer Festigkeit verbessert die Energieeffizienz und Langlebigkeit der Fahrzeuge.
In der Umwelttechnik kommen heißgepresste GFK-Bauteile insbesondere dort zum Einsatz, wo hohe Korrosionsbeständigkeit gefordert ist, etwa als Gehäuse für Rauchgas-Filteranlagen, chemikalienbeständige Behälter oder Abdeckungen in Kläranlagen. Die lange Lebensdauer und Beständigkeit gegenüber aggressiven Medien machen GFK hier zur wirtschaftlichen Alternative zu Metallkomponenten.
Qualitätssicherung beim Heißpressen: Prüfverfahren für GFK-Bauteile
Die Qualitätssicherung ist ein zentraler Bestandteil der Fertigung. Eine lückenlose GFK-Prüfung stellt sicher, dass jedes Bauteil den Spezifikationen entspricht. Zum Einsatz kommen dabei:
Zerstörungsfreie Prüfung (ZfP): Verfahren wie Ultraschall und Thermografie detektieren innere Fehlstellen wie Lufteinschlüsse oder Delaminationen, ohne das Bauteil zu beschädigen.
Mechanische Prüfverfahren: Zug- oder Biegeversuche an Probekörpern dienen dem direkten Festigkeitsnachweis und validieren die mechanischen Kennwerte des Materials.
Bildgebende Analysen: Die Computertomographie (CT) ermöglicht eine präzise Kontrolle der Faserorientierung und der homogenen Materialverteilung, was für die Performance des Bauteils entscheidend ist.
Alle Prozessdaten (Druck, Temperatur, Zeit) werden zudem geloggt, um eine vollständige Rückverfolgbarkeit jeder Charge zu gewährleisten.
Zukunft des GFK-Heißpressens: Innovationen & neue Materialien
Die Entwicklung im Bereich der heißgepressten GFK-Bauteile zielt aktuell auf die Integration von thermoplastischen Harzsystemen, die kürzere Zykluszeiten und verbesserte Recyclingmöglichkeiten bieten. Zudem werden hybride Werkstoffe erforscht, die lokale Verstärkungen durch Carbonfasern mit den Vorteilen von GFK verbinden. Digitale Technologien ermöglichen eine fortschrittliche Prozesssteuerung und Qualitätssicherung, während integrierte Sensorik während des Pressvorgangs neue Funktionen und Zustandsüberwachungen erlaubt.
Beschaffung & Partner: GFK heißgepresst zuverlässig liefern
Trade World One unterstützt Kunden in Verkehrs- und Umwelttechnik mit solider Materialexpertise und einem globalen Netzwerk zertifizierter Hersteller für heißgepresste GFK-Bauteile. Durch unser umfassendes technisches Verständnis und ein leistungsfähiges Logistikzentrum sichern wir die schnelle Verfügbarkeit auch von komplexen oder obsoleten Komponenten. Wir bieten individuelle Beschaffungslösungen einschließlich Reverse Engineering, um die Betriebssicherheit und Lebensdauer Ihrer Anlagen zu gewährleisten. Unsere Expertise macht uns zum idealen Partner für anspruchsvolle GFK-Beschaffung.
Fazit: Warum heißgepresstes GFK die richtige Wahl ist
GFK heißgepresst vereint die Vorteile moderner Verbundwerkstoffe mit einem effizienten Fertigungsverfahren, das sich ideal für vielfältige technische Anwendungen eignet. Die Kombination aus Leichtbau, Robustheit und Wirtschaftlichkeit positioniert dieses Material als Schlüsseltechnologie für zukunftsorientierte Industriepartner wie Trade World One und deren Kunden.
Quellen
- Glasfaserverstärkte Kunststoffe (GFK) – Wikipedia
- Glass Fiber Reinforced Plastics – ScienceDirect
- Glasfaserverstärkte Kunststoffe – Springer
- What is Glass Fiber Reinforced Plastic? – Materials Today
- Glass Fiber Reinforced Polymer Properties
- Glass Fiber Reinforced Polymer Composites for Structural Applications – Elsevier
- Glass Reinforced Plastics – ScienceDirect
- Fiber Reinforced Polymer – Wikipedia
- Glass Fiber Reinforced Composites – ChemistryViews
- Advantages of Glass Fiber Reinforced Plastics – Materials Today
Haben Sie Fragen? Treten Sie gerne jederzeit mit uns in Kontakt.
Zur Kontaktseite